In the midstream oil and gas industry, where operational efficiency and safety are critical, real-time data has become a game-changer. The industry faces numerous challenges, including harsh environments, high-risk operations, and complex logistics.
In this context, the ability to access, analyse, and act on data instantly can significantly improve safety, optimise production, reduce costs, and enhance decision-making processes.
Traditionally, data in midstream oil and gas operations was collected and processed offline, leading to delays in identifying potential issues and making critical decisions. However, with the advancement of Internet of Things (IoT) sensors, advanced analytics, and cloud computing, real-time data has revolutionised how companies manage operations on both onshore and offshore sites.
By harnessing real-time data, midstream oil and gas operators can monitor equipment performance, track operational processes, and detect anomalies as they happen. This proactive approach allows for quicker responses to problems, ensuring workers' safety and operations' efficiency.
In this blog, we will explore how integrating real-time data into various aspects of oil and gas operations improves safety standards, reduces downtime, and increases productivity while driving cost-effective solutions across the sector.
#The Role of Real-Time Data in Safety
Safety is paramount in the midstream oil and gas industry, where the consequences of equipment failure or operational hazards can be catastrophic. Real-time data plays a critical role in ensuring that operations are conducted safely.
They enable constant monitoring, early detection of potential hazards, and the ability to respond instantly to critical situations.
Let's break down the ways real-time data enhances safety:
Monitoring Pipeline Pressure and Flow Rates
Pipelines are prone to leaks, ruptures, or pressure fluctuations that could pose significant environmental and safety risks. Operators can continuously monitor pipeline pressure, flow rates, and temperature at various points using real-time data from sensors embedded along the pipeline.
Suppose there’s an anomaly in pressure or flow, such as a sudden drop in pressure or an abnormal increase in flow. In that case, the system can instantly alert operators to potential problems, such as leaks or blockages.
Early detection of pressure irregularities can help prevent disasters such as pipeline ruptures, reducing the risk of environmental spills, fire hazards, and worker injuries.
By automating this monitoring, operators don’t need to rely on periodic manual checks. Real-time data allows for 24/7 monitoring, providing peace of mind for both operational teams and the communities surrounding pipeline infrastructure.
Predictive Maintenance to Prevent Failures
Predictive maintenance (PdM) is a method that uses real-time data collected from sensors to predict when equipment or machinery is likely to fail. In the midstream oil and gas industry, where machinery such as pumps, valves, and compressors are constantly used, unplanned downtime can be expensive and dangerous.
Sensors on equipment track key parameters such as vibration, temperature, and pressure. By analysing this data, companies can predict when equipment will require maintenance before a failure occurs.
Real-time data allows operators to plan maintenance proactively. This reduces costs associated with unscheduled repairs and minimises the risk of equipment failures that could lead to hazardous situations, such as fires or explosions.
Immediate Response to Safety Incidents
When a safety incident occurs in oil and gas operations, response time is critical to preventing further damage and ensuring personnel safety. Real-time data enables immediate responses to such incidents.
Real-time data systems can trigger immediate alarms when sensors detect hazardous conditions, such as gas leaks or abnormal equipment behavior, enabling operators to take quick action.
In a severe anomaly, real-time data can automatically trigger shutdown protocols or initiate emergency systems, such as venting or fire suppression mechanisms, reducing the risk of catastrophic events.
Real-time monitoring allows for more informed decision-making during emergencies. Operators can track the progression of a safety incident in real-time and make critical adjustments to evacuation plans, firefighting efforts, or other safety protocols as the situation evolves.
#Operational Efficiency Gains from Real-Time Data
In the midstream oil and gas industry, maximising operational efficiency is crucial to staying competitive and profitable. Real-time data plays a vital role in enhancing productivity, optimising asset performance, and ensuring that every part of the operation runs smoothly.
Below are key ways in which real-time data drives operational efficiency:
Reducing Downtime and Optimising Asset Performance
Unplanned downtime in oil and gas operations can be extremely costly, both in terms of lost production and repair expenses. Real-time data facilitates predictive maintenance and more informed decision-making, which helps reduce equipment failure and optimise asset performance.
By continuously monitoring equipment condition using real-time data from sensors, operators can predict when components are likely to fail. Real-time data also helps operators monitor asset performance against optimal benchmarks.
Operators can identify opportunities to fine-tune machinery settings, ensuring that assets operate at peak efficiency, reducing waste, and enhancing production capacity. Identifying problems early allows operators to address them before they escalate into costly repairs or catastrophic failures.
Enhancing Supply Chain and Logistics Management
The logistics of transporting materials, equipment, and personnel are complex, as they often require coordination between multiple stakeholders and resources spread across vast distances. Real-time data helps streamline these operations, improving the efficiency of supply chains and logistics management.
With real-time tracking of shipments, materials, and equipment, operators can gain full visibility into the supply chain. This allows them to track delivery times, monitor transportation conditions and anticipate potential disruptions.
Operators can avoid shortages and overstocking by using real-time data to track inventory levels. Real-time monitoring enables better demand forecasting and more accurate ordering, reducing delays and lowering the costs associated with excess inventory.
Real-time data can also be used to manage personnel logistics, ensuring workers are efficiently deployed across operations. It can track when workers are scheduled for shifts, their proximity to operational sites, and any requirements for crew changes.
Regulatory Compliance and Reporting Automation
The midstream oil and gas industry is heavily regulated, with strict standards set by government agencies for environmental impact, safety, and operational procedures. Real-time data is important in ensuring that operators remain compliant and can automate the reporting process.
Real-time data helps monitor key compliance metrics, such as emissions levels, water usage, or hazardous material handling, ensuring that operations adhere to environmental regulations.
The time-consuming process of generating compliance reports can be automated using real-time data. With integrated data systems, compliance reports are generated automatically based on live data feeds.
Automating compliance and reporting tasks reduces the risk of human error in manual data entry and reporting. Real-time data integration ensures that the right data is recorded, analysed, and presented accurately in compliance reports, making audits easier and faster.
#Technologies Enabling Real-Time Data Collection & Analysis
The increasing reliance on real-time data in oil and gas operations is fueled by advances in technology. These innovations provide operators with the tools necessary to gather, process, and analyse vast amounts of data quickly and efficiently.
Let’s explore these key technologies in more detail:
IoT Sensors
The Internet of Things (IoT) has revolutionised the way data is collected in real-time. In midstream oil and gas operations, IoT sensors are deployed across various assets, machinery, pipelines, and environmental monitoring systems to provide continuous, real-time insights into operational conditions.
IoT sensors are capable of capturing a wide range of operational data, including pressure, temperature, flow rates, vibration, and gas composition. These sensors are installed directly on equipment or at critical points in pipelines, rigs, or tanks.
IoT sensors allow for remote monitoring of equipment in real-time, reducing the need for physical presence while ensuring that operators can track conditions from a centralised control room or even on mobile devices.
AI-Driven Predictive Analytics
AI-driven predictive analytics leverages the power of machine learning and advanced algorithms to analyse historical and real-time data in order to forecast potential future events or issues.
AI can analyse real-time data from IoT sensors and historical maintenance records to predict when equipment is likely to fail. By identifying patterns and anomalies, AI models can generate maintenance schedules that reduce the risk of unplanned downtime and mitigate safety hazards.
AI-powered tools can forecast production levels based on real-time operational data and market trends. Additionally, AI can simulate different operational scenarios to predict outcomes under various conditions, enabling better decision-making and planning.
Cloud-Based SCADA Systems
Supervisory Control and Data Acquisition (SCADA) systems are used to monitor and control industrial operations remotely. Cloud-based SCADA systems are a major innovation in the midstream oil and gas industry, providing greater flexibility, scalability, and efficiency in managing large, dispersed operations.
Cloud-based SCADA systems, however, store data remotely on cloud servers, making it accessible from anywhere. This centralisation allows operators to monitor real-time data from all operational sites, regardless of location and enables global coordination.
Cloud-based SCADA systems allow operators to view real-time operational data and control equipment remotely, making it easier to respond to issues immediately.
Cloud-based SCADA systems enable vast amounts of data to be collected, stored, and processed without the limitations of on-site infrastructure. This flexibility allows midstream oil and gas companies to scale their monitoring and data collection efforts as their operations grow.
Cloud-based SCADA systems can integrate with other data analytics tools and technologies. This facilitates the use of AI and machine learning algorithms to process data in real-time, enhancing predictive capabilities, process optimisation and anomaly detection.
#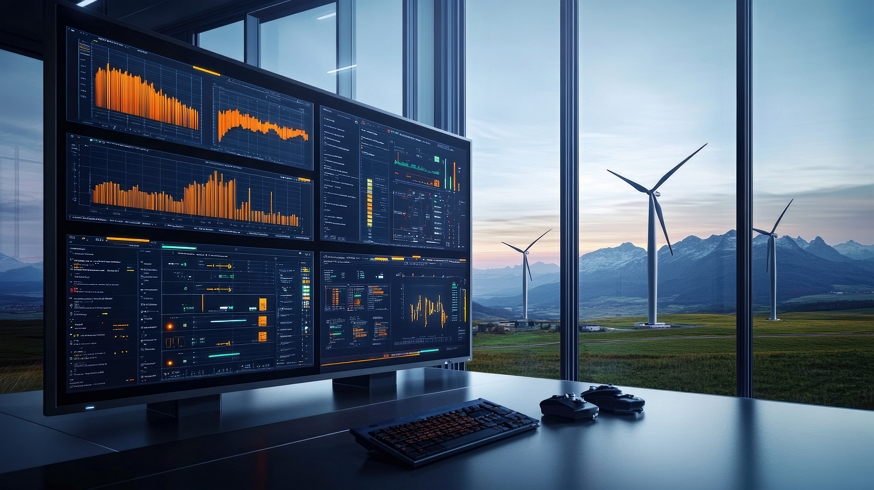
Challenges of Implementing Real-Time Data Systems
While real-time data systems offer immense benefits in improving safety, operational efficiency, and decision-making in the midstream oil and gas industry, their implementation comes with several challenges.
Let’s look at some of the following challenges:
Data Integration and Infrastructure Requirements
Integrating real-time data into existing operations can be a complex and resource-intensive process. Oil and gas companies often work with legacy systems, machinery, and equipment that were not designed to communicate with modern data collection technologies.
Integrating new IoT sensors, AI-driven analytics, and cloud-based SCADA systems with these existing systems can be time-consuming and costly.
Real-time data systems generate massive amounts of data, which can be overwhelming to manage and analyse. Ensuring that the data is accurate, high-quality, and free from noise is critical. Additionally, managing the sheer volume of data from multiple sensors and systems requires significant computing power and storage capacity.
As operations expand or new technology is introduced, the infrastructure supporting real-time data systems must be able to scale accordingly. In many cases, scaling up infrastructure can be costly and technically challenging, especially for companies with global or offshore operations.
Cybersecurity Considerations
The adoption of real-time data systems also introduces a new set of cybersecurity challenges. As more data is collected, transmitted, and stored online, the risk of cyberattacks increases.
The integration of IoT sensors, cloud-based systems, and connected infrastructure creates numerous potential entry points for cybercriminals. Each device, system, or connection point could become a target for attack.
With real-time data flowing constantly, ensuring that data is encrypted both in transit and at rest is essential to prevent breaches. Additionally, securing cloud-based systems requires continuous monitoring and updates to avoid vulnerabilities.
Cyberattacks targeting industrial control systems (ICS) or SCADA systems could lead to operational disruptions, such as equipment shutdowns, production halts, or even safety incidents.
Ensuring that real-time data systems are protected from cyber threats is not just a matter of safeguarding company assets, but also protecting the safety and well-being of workers and communities.
#Conclusion
Real-time data is fundamentally reshaping midstream operations in the oil and gas industry, driving greater efficiency, safety, and profitability. Integrating real-time data into these operations is transforming how these challenges are approached, enabling operators to make faster, more informed decisions and respond to issues proactively.
By adopting technologies like IoT sensors, AI-driven predictive analytics, and cloud-based SCADA systems, midstream oil and gas companies can continuously monitor pipeline conditions, optimise asset performance, and minimise operational downtime.
On the logistics front, real-time data improves supply chain visibility, helping operators track materials, shipments, and personnel more accurately. This level of visibility allows for better coordination and scheduling, reducing delays and improving overall operational efficiency.
Real-time data revolutionizes midstream oil and gas operations, providing greater control, efficiency, and safety across the energy supply chain. By embracing these technologies, midstream operators can optimise performance, mitigate risks, reduce costs, and enhance overall operational excellence; whilst meeting the growing demands of the modern energy landscape.
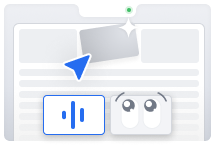