In the face of global energy demand, increasing environmental regulations, and the constant push for operational excellence, the oil and gas industry is undergoing a digital revolution.
One of the most significant transformations is taking place in gas processing plants, where cutting-edge technologies like the Internet of Things (IoT), Artificial Intelligence (AI), and cloud computing are reshaping the way facilities operate. These innovations are not only streamlining processes but also redefining what it means to run a smart gas processing plant.
This article explores the key elements that make a gas processing plant smart, and how digital technologies are driving improvements in predictive maintenance, emissions monitoring and overall plant performance.
#What Makes a Gas Processing Plant Smart?
Traditional gas processing plants rely heavily on manual oversight, periodic inspections and reactive maintenance strategies. In contrast, a smart gas processing plant integrates digital technologies across its infrastructure to enable:
Real-time monitoring of plant performance
Predictive analytics for maintenance and optimization
Remote operations and centralized data management
Automation of repetitive or high-risk tasks
The result is a plant that not only reacts faster to operational issues but often prevents them entirely; minimizing downtime, reducing operational costs and enhancing safety and compliance.
#IoT Sensors: The Foundation of Smart Monitoring and Control
At the heart of any smart plant is a network of IoT sensors. These sensors are deployed across key assets (compressors, valves, pipelines, heat exchangers and more) to collect continuous data on variables like pressure, temperature, vibration, flow rate and emissions.
Key Benefits of IoT in Gas Plants:
Real-Time Data Acquisition: Operators gain minute-by-minute insight into the plant’s health and performance.
Remote Monitoring: Field operations can be viewed from centralised control rooms or even mobile apps.
Anomaly Detection: Early warning systems can alert teams to potential equipment failures or dangerous conditions.
This level of granular, real-time visibility is essential not only for operational efficiency but also for safety-critical applications like emissions monitoring in oil and gas environments.
For a better insight into how IoT helps in the optimization of plant data, please refer to the following blog: “Unlocking Plant Data”.
#AI-Driven Predictive Maintenance and Optimization
One of the most impactful applications of smart technology in gas plants is AI-driven predictive maintenance. Traditional maintenance strategies follow fixed schedules or respond to failures after they occur.
Predictive maintenance, by contrast, uses AI algorithms to analyze historical and real-time sensor data, identifying patterns that precede failures.
How AI Enhances Maintenance:
Predictive Algorithms: Machine learning models anticipate when equipment is likely to fail, enabling proactive maintenance scheduling.
Root Cause Analysis: AI helps diagnose not just that something will go wrong, but why; enabling targeted fixes.
Optimized Resource Use: Maintenance crews are dispatched only when and where needed, reducing labor costs and minimizing production interruptions.
For example, a predictive maintenance gas plant implementation might detect subtle changes in compressor vibration patterns, indicating bearing wear weeks before a failure. The plant can then schedule maintenance during a planned downtime rather than experiencing costly unplanned outages.
Beyond maintenance, AI is also being used to optimize processing operations. By learning from vast data sets, AI systems can recommend adjustments to parameters like temperature or flow rate to maximize throughput, reduce energy consumption or improve product quality.
#Cloud-Based Integration for Centralized Data Visibility
While IoT sensors and AI analytics operate at the edge, the cloud brings it all together. Cloud platforms provide a centralized environment to store, analyze and share data across multiple plant locations or even across an entire organization.
Advantages of Cloud Integration:
Scalability: Add new sensors or connect additional plants without massive infrastructure upgrades.
Cross-Site Collaboration: Engineering teams, analysts, and decision-makers can access unified dashboards from anywhere.
Advanced Analytics: Cloud computing enables heavy data processing, such as AI model training and large-scale trend analysis.
Data Security and Backup: Cloud providers offer robust cybersecurity measures and automated backups, reducing the risk of data loss or cyber threats.
This centralized approach enables leadership to gain a holistic view of operations, identify systemic issues, and drive strategic improvements throughout the organization.
To gain a better insight into cloud integration, please refer to the following blog: “Future of IoT in Oil and Gas”.
#Improved Safety, Emissions Reduction and Compliance
Beyond operational efficiency, smart technologies play a critical role in improving environmental and safety outcomes. With increased public and regulatory scrutiny, emissions monitoring in oil and gas has become a top priority.
Smart Plants Support:
Continuous Emissions Monitoring (CEMS): Real-time data helps ensure compliance with environmental standards and enables faster response to leaks or exceedances.
Leak Detection and Repair (LDAR): Smart sensors can detect fugitive emissions from equipment before they escalate.
Safety Automation: Automated shutdowns, alarms, and interlocks triggered by sensor data reduce the risk of human error and accidents.
AI can also analyze safety incident data to predict high-risk scenarios, further enhancing worker protection. These capabilities help operators meet regulatory requirements while also supporting sustainability goals.
For further insight on the journey towards smart systems, please refer to the following blog: “From Spreadsheets to Smart Systems”.
#Example: Achieving Uptime and Efficiency Gains
Let’s consider a mid-sized gas processing facility in Texas that implemented a smart plant solution integrating IoT, AI and cloud technologies.
Initial Challenges:
Frequent compressor downtime (average of 9 hours/month)
Limited visibility into emissions data, making regulatory reporting labor-intensive
High maintenance costs due to reactive service models
Smart Technology Deployment:
Over 300 IoT sensors installed across critical assets
AI-based predictive maintenance platform connected to vibration, temperature and flow data
Cloud-based dashboard provided real-time data visualisation and historical analysis
Emissions sensors tied to a compliance reporting platform
Results After 12 Months:
Compressor downtime reduced by 68%, adding approximately 70 operational hours annually
Maintenance costs dropped by 24% thanks to better scheduling and fewer emergency interventions
Regulatory reporting time decreased by 80%, enabling faster audits and compliance checks
Energy efficiency improved by 12% due to AI-optimized processing set points
This example illustrates how smart technologies do more than digitize; they transform operations in ways that directly improve the bottom line and environmental performance.
#Conclusion: The Future is Smart and Already Here
As the oil and gas sector grapples with aging infrastructure, volatile markets and increasing regulatory pressure, the case for smart gas processing plants is stronger than ever.
With IoT providing the eyes and ears, AI offering the brainpower, and the cloud acting as the central nervous system, modern plants are evolving into intelligent ecosystems.
From predictive maintenance in gas plants to real-time emissions monitoring and energy optimization, the benefits are tangible, measurable and mission-critical.
The future of gas processing is not just digital; it’s smart, efficient, safe and sustainable.
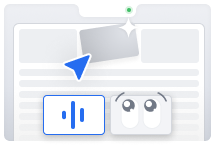
Table of contents
- What Makes a Gas Processing Plant Smart?
- IoT Sensors: The Foundation of Smart Monitoring and Control
- AI-Driven Predictive Maintenance and Optimization
- Cloud-Based Integration for Centralized Data Visibility
- Improved Safety, Emissions Reduction and Compliance
- Example: Achieving Uptime and Efficiency Gains
- Conclusion: The Future is Smart and Already Here