Natural Gas Liquids (NGLs) are a group of hydrocarbons found in natural gas that exist as liquids under normal temperature and pressure. These include ethane, propane, butanes, and natural gasoline.
NGLs play a crucial role in the energy sector, serving as essential feedstocks for petrochemical production, fuels for heating and transportation, and components in various industrial applications.
One of the key processes in unlocking the full potential of NGLs is fractionation. This is the process of separating NGLs into individual components based on their boiling points. Fractionation is vital in ensuring that different products are available in the right quantities and qualities for various uses.
In this blog, we will look at the fractionation process and its importance to the processing and value optimization of NGLs.
Whether you’re new to the energy sector or looking to deepen your knowledge, this guide will help demystify the fractionation process and its critical role in the NGL supply chain.
What Are Natural Gas Liquids (NGLs)?
Natural Gas Liquids (NGLs) are hydrocarbons found within natural gas that exist as liquids, unlike methane. They are heavier and can be separated from the natural gas stream through a process called fractionation.
Some common types of NGLs include:
- Ethane
- Propane
- Butane
- Isobutane
- Natural Gasoline
In industrial settings, NGLs are integral to the production of petrochemicals, plastics, and synthetic rubber. In consumer markets, they provide everyday fuels like propane for heating and butane for portable stoves or lighters.
These liquids also contribute to the refinement of gasoline, boosting fuel efficiency and performance. In essence, NGLs are an indispensable part of both energy production and industrial manufacturing.
Why Is Fractionation Necessary?
When natural gas is initially extracted from the earth, it often contains a mixture of gases. This mixed stream is known as raw natural gas. Although the mixed components have significant value individually, their presence as a mixture creates several challenges for both transport and use.
Transporting and using NGLs in their mixed form can be inefficient and problematic for a few reasons:
- Storage and Handling Issues: Different NGLs have distinct physical properties, so it can be difficult to store them at the right temperature and pressure.
- Quality Control for Specific Applications: Many industries require specific NGLs in pure form. Without separation, it becomes challenging to meet the standard product needed for use.
- Transport Efficiency: Moving a mixed stream of NGLs in pipelines can be difficult, as different components will behave differently under the same conditions.
On the other hand, the benefits of fractionating NGLs include:
- Enhanced Utilisation: Once separated, each NGL can be processed or transported in the most efficient manner for its intended use.
- Improved Market Flexibility: By creating pure components, fractionation enables producers to respond more effectively to market demands.
- Optimized Transport and Storage: Fractionated NGLs can be more easily transported and stored in bulk because each component has distinct physical properties.
- Maximized Value: Separating NGLs ensures that each product is used in its most valuable and appropriate application.
The Fractionation Process: Step-by-Step
Overview of Fractionation
Fractionation is the process used to separate a mixture of NGLs into its individual components based on differences in their boiling points.
Temperature plays a critical role in fractionation. By precisely adjusting the temperature in the column, the separation of NGLs is achieved based on the principle that each liquid has a unique boiling point at a given pressure.
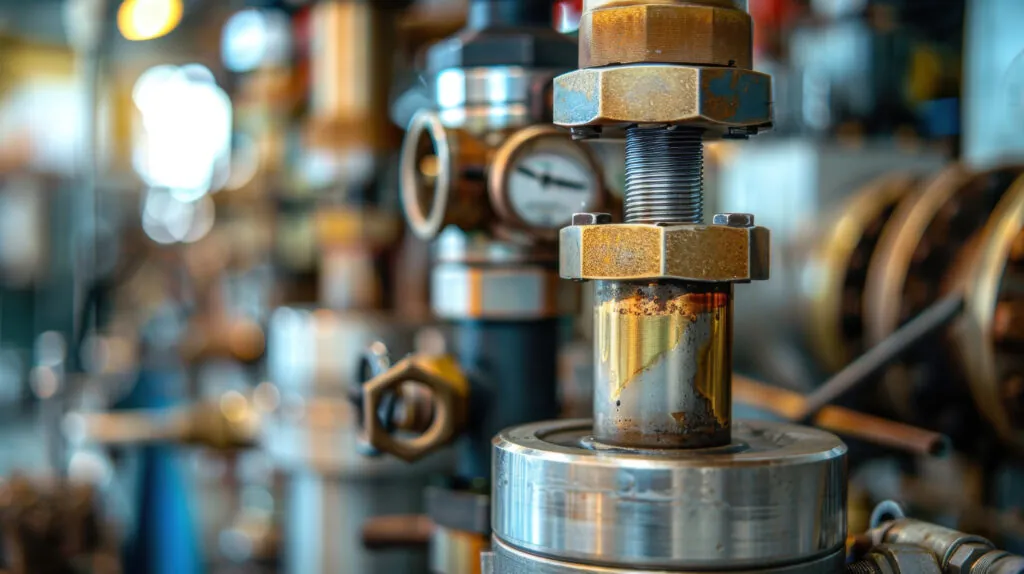
Steps in the Fractionation Process
Fractionation involves several key steps that occur in a series of distillation columns, where the mixture of NGLs is progressively separated.
Below are the primary steps involved:
- Deethanization
Here the mixture of NGLs is cooled to a temperature where ethane can be separated from the other heavier hydrocarbons. Ethane has the lowest boiling point of the NGL components, so it condenses first.
- Depropanisation
In this step, propane is isolated from the heavier butanes and natural gasoline. Since propane boils at -42°C (-44°F), it condenses at a higher temperature than ethane, but lower than butane.
- Debutanisation
This process isolates the butanes from natural gasoline. The butane component has two varieties: normal butane and isobutane, each with slightly different boiling points.
- Butane-isomerization
Once these are separated, some refineries may choose to carry out butane-isomerization to convert normal butane into isobutane. Isobutane has a higher octane rating, making it more useful for refining gasoline.
- Natural Gasoline Recovery
The remaining liquid now contains natural gasoline, a mixture of heavier hydrocarbons. These heavier components are typically recovered as natural gasoline or condensate.
Technology and Equipment Used in Fractionation
The technology and equipment used in fractionation have evolved significantly, leading to increased efficiency and precision.
The key equipment consists of:
- Fractionation Towers (or Distillation Columns): The tower is a vertical cylindrical structure packed or fitted with trays to enhance the separation of components. They separate components of a mixture based on their boiling points.
- Reboilers: These are used to supply the necessary heat to the bottom of the fractionation column to promote vaporization.
- Condensers: They cool the vaporized components coming from the top of the fractionation tower.
- Storage Tanks: These are typically large and well-sealed to prevent contamination and loss of volatile components. The different fractions of the mixture are stored in tanks for further processing or sale.
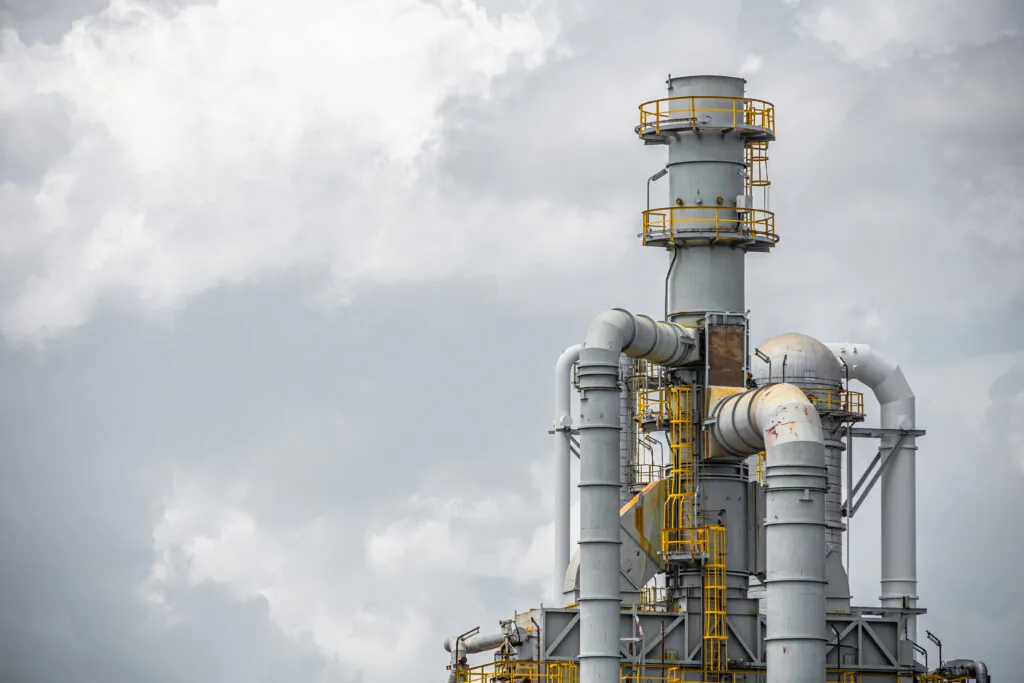
Innovations in technology allow for greater precision, energy savings, and overall improved efficiency in fractionation. These include:
- Automation:
Distributed Control Systems (DCS) and Supervisory Control and Data Acquisition (SCADA) systems, enable real-time monitoring and control of the fractionation process. This allows for precise regulation of temperature, pressure, and flow rates to optimize separation efficiency.
- Process Optimization:
The use of advanced control strategies like Model Predictive Control (MPC) helps optimize the fractionation process by predicting the outcomes of changes in parameters and adjusting in real time for maximum efficiency.
Challenges in Fractionation
Energy-Intensive Nature of the Process
Since fractionation requires heating and cooling of different hydrocarbons, this process can be energy-demanding. It involves significant amounts of heat exchange and refrigeration. The energy cost can be a major part of the overall operating expenses.
Environmental Concerns and Emissions
Fractionation plants are associated with emissions, including greenhouse gases like CO2, as well as volatile organic compounds (VOCs). The combustion of fossil fuels for the heat required in fractionation can contribute to air pollution and climate change.
Economic Considerations
The demand for NGLs can fluctuate based on market conditions, which impacts the profitability of fractionation operations. For instance, economic slowdowns, shifts in energy demand, or competition from alternative energy sources can influence NGL prices.
Applications and End-Uses of Fractionated NGLs
The fractionated NGLs have different applications as mentioned below:
Ethane
- Ethane is primarily used as a feedstock for ethylene production in steam crackers.
- Ethylene is a key raw material for producing plastics (like polyethylene), and chemicals, such as ethylene glycol (used in antifreeze) and ethylbenzene (used to make styrene for plastics).
Propane
- Propane is widely used as a clean-burning fuel for heating homes, water heating, and cooking, especially in rural areas.
- It is used as an alternative fuel for cars, buses, and trucks.
- Also, it is used in various industrial processes, such as metal cutting, and as a fuel in engines and industrial heaters.
Butane
- They are used as refining feedstock to produce other fuels and chemicals, or blended with other hydrocarbons to produce motor fuels.
- These are commonly used in aerosol products, including spray paints, deodorants, and cleaning agents, due to its ability to vaporize quickly and easily.
- Butanes are also used in the production of synthetic rubber, which is essential for manufacturing tires, footwear, and various automotive components.
Natural Gasoline
- Natural gasoline is used to dilute heavy crude oils to make them easier to transport via pipelines.
- It is sometimes blended with gasoline to improve the fuel’s performance characteristics, such as volatility and combustion efficiency.
Environmental and Economic Impacts
The environmental and economic impacts of the fractionation process are significant, especially as industries look to balance energy demands with sustainability goals.
Improving the energy efficiency of fractionation is a priority. For that purpose, heat integration is used, where the heat from one part of the process is used to preheat other streams in the system. This reduces the need for external heating sources.
Moreover, process intensification is being used to optimize the fractionation process. This is done by using smaller, more efficient equipment that achieves the same or better performance with lower energy consumption.
The strategies being used to reduce greenhouse gas emissions involve the implementation of carbon capture and storage. Through greenhouse gas monitoring, the emissions throughout the fractionation process can be monitored, which will help companies identify areas for improvement.
Furthermore, the economic benefit to energy companies is that it is a source of revenue generation. As fractionation adds value by converting raw natural gas into valuable NGLs, so by producing a range of NGLs fractionation plants can cater to multiple markets.
The economic benefit to consumers is that fractionation produces valuable byproducts, which can be sold at competitive prices. This leads to lower energy costs for consumers. Also, the ability to produce and separate NGLs locally adds energy security, reducing dependence on imported fuels.
Future Trends in Fractionation
The future of fractionation is essentially tied to global shifts in energy demand, technological innovation, and sustainability goals. The move towards cleaner, more efficient technologies in NGL separation will ensure its relevance in energy markets.
Also, with increasing global demand for NGLs, the future will maintain its enduring significance of fractionation in both traditional and emerging energy markets.
Additionally, its potential role in supporting hydrogen production and renewable energy systems opens up exciting possibilities for fractionation in the clean energy transition.