In midstream oil and gas, artificial lift system plays a crucial role in ensuring the continuous flow of hydrocarbons to the surface, especially when natural reservoir pressure is insufficient to drive production.
These systems are designed to supplement the pressure from the reservoir and increase the production rate by lifting the fluid from the wellbore to the surface. They are essential in maintaining well performance over time, optimising production rates, and extending a well's lifespan.
Choosing the right artificial lift system is critical for operators, as the wrong choice can lead to inefficiencies, high operational costs, or even premature well failure. Operators face numerous challenges, including well characteristics, cost constraints, and equipment reliability, which can complicate the decision-making process.
This blog aims to provide a comprehensive guide to help operators navigate the complexities of artificial lift system selection. By addressing the key factors influencing system choice and highlighting the most common challenges, we will empower you to make more informed decisions that optimize production and reduce costs.
#What Is an Artificial Lift System?
An artificial lift system is a mechanical method for enhancing the flow of fluids from a wellbore to the surface.It supplements the reservoir’s ability to naturally produce hydrocarbons, maintaining or increasing the well’s production rate.
Artificial lift systems improve well performance, extend the life of a well, and maximise the extraction of hydrocarbons from a reservoir. These systems are often employed after the natural pressure has decreased due to depletion, water influx, or other factors. They ensure that production continues at a desirable rate.
Artificial lift systems enhance oil recovery by maintaining good pressure. The lift helps keep the pressure in the wellbore at a level that is sufficient to overcome the resistance of the column of oil and gas. This allows production to continue even as the natural reservoir pressure declines.
By supplementing the natural pressure, artificial lift systems help boost the flow rate, particularly in mature fields or when the reservoir pressure is too low to achieve optimal production.Artificial lift is a critical component in the oil and gas industry. It is estimated that more than 80% of oil wells worldwide require some form of artificial lift. The industry relies heavily on artificial lift, especially in mature fields, which often experience declining pressure, making natural flow insufficient.
#Key Considerations When Choosing an Artificial Lift System
Selecting the right artificial lift system involves assessing several key factors. Below are the primary considerations operators must evaluate when choosing an artificial lift system.
Well Conditions
The characteristics of the well itself significantly impact which artificial lift system is the most appropriate choice. Operators must evaluate several factors related to the well’s conditions:
Reservoir Depth: The deeper the well, the more challenging lifting fluids to the surface becomes. Deep wells typically require more robust artificial lift systems, such as electric submersible pumps (ESPs), as they can handle the higher lifting requirements.
Pressure and Temperature: Wells with high-pressure reservoirs need systems designed to handle high pressure and temperature, like ESP systems or plunger lifts.
Fluid composition: The characteristics of the fluids produced from the well can vary widely, and each lift system is suited to particular fluid types such as:
Oil: Rod pumps or ESP systems are often preferred for oil-rich wells with little gas or water.
Gas: Wells with a high gas-to-oil ratio may benefit from gas lift systems injecting gas into the wellbore.
Water Cut: High water cuts require systems capable of handling larger volumes of water, such as ESP systems or progressive cavity pumps (PCPs).
Solids: Wells with significant amounts of solids (sand, debris) require systems like plunger lifts or progressive cavity pumps (PCPs).
Production rate expectations: The desired production rate is another key factor that influences the choice of an artificial lift system. Different systems are better suited for different levels of production such as high, moderate, and low.
Lifecycle of the Well
Early Production Stage: The main goal in this phase is to establish stable production, so rod pumps or gas lift systems might be effective.
Middle Production Stage: As production rates begin to decline, operators often turn to ESP systems, progressive cavity pumps (PCPs), or plunger lifts.
Late Production Stage: The production rate has often fallen significantly, so lift systems must be adapted for lower production volumes and increased water content. Plunger lifts and gas lift systems are often ideal during this stage.
Scalability and Adaptability: The chosen system must be scalable and adaptable to accommodate fluctuations in production. It should allow for easy upgrades, such as adding more stages in a pump or adjusting to deeper or shallower reservoir depths over time. Flexibility is key as the well’s conditions change throughout its lifecycle.
Environmental and Economic Factors
These considerations are among the most important when choosing an artificial lift system, as they directly impact operations' cost and sustainability.
Operating and Capital Costs: Capital costs refer to the initial setup costs of purchasing and installing the system while operating costs involve day-to-day maintenance, energy consumption, and replacement parts.
Energy Efficiency and Environmental Impact: Artificial lift systems that consume less energy tend to have a smaller carbon footprint, contributing to more sustainable operations.
Maintenance and Reliability: Systems that are easier to maintain and have fewer breakdowns can help reduce downtime and improve production efficiency.
Location and Infrastructure
The specific location of the well and available infrastructure can influence the choice of an artificial lift system.
Proximity to Power Sources: Some systems require a reliable source of electricity to operate effectively. If the well site is far from power sources or located in a remote area, this could limit the viability of certain systems.
Availability of Skilled Labor: More complex systems require highly skilled labor for installation, operation, and maintenance.
Space constraints at the well site: If significant space constraints exist, it may be difficult to install and operate larger systems requiring large surface equipment.
#Overview of Common Artificial Lift Systems
Some of the common artificial lift systems are discussed below.
Beam Pump (Sucker Rod Pump)
This is one of the most widely used artificial lift systems, especially in low- to medium-production oil wells. It operates through the mechanical movement of a sucker rod that is driven by a pump jack (the beam).
The system uses a combination of reciprocating motion and mechanical components to lift fluid from the reservoir.
The key components include:
1. Pump Jack (Beam): This surface unit provides the mechanical motion. It’s typically powered by a motor and converts rotational motion into up-and-down motion.
2. Sucker Rods: These are long metal rods that extend from the surface pump jack down into the wellbore, where they connect to the pump mechanism at the bottom of the well.
3. Downhole Pump: The pump is located at the bottom of the well. It consists of a plunger and valves that control the flow of fluid.
4. Pump Rod: The pump rod is the section of the sucker rod that connects the downhole pump to the surface equipment.
5. Power Source: The motor driving the pump jack can be powered by electricity, gas, or diesel, depending on the location and available resources.
Ideal Well Conditions for Beam Pumps
Beam pumps are most effective in wells with specific conditions. These include:
Shallow to Moderate Depths: Due to their mechanical limitations, beam pumps are generally best suited for shallow or moderate-depth wells (typically up to 2,500 feet).
Low to Moderate Reservoir Pressure: They work well in wells where the reservoir's natural pressure is insufficient to bring oil to the surface on its own.
Viscous Fluids: They are ideal for lifting heavier, more viscous fluids, including crude oil with high viscosity.
Stable Production Rates: They are best suited for wells with steady, continuous production. They are less effective in wells with highly fluctuating production rates.
Low to Moderate Gas-to-Oil Ratio: They are less efficient when a well has a high gas-to-oil ratio. The system could become less effective if gas interferes with the pump’s ability to lift oil.
Advantages:
Cost-Effective: Beam pumps are economical to install and operate.
Simple and Reliable: They have been used in the oil industry for decades and are known for their reliability.
Suitable for Viscous Fluids: The mechanical design of the sucker rod pump is ideal for lifting thicker, more viscous oils.
Scalable: They can be easily scaled by adding or adjusting the number of strokes per minute or changing the plunger size.
Widely Available: Parts and components for beam pumps are readily available, and many service companies are skilled in their operation.
Limitations:
Limited Depth: They are unsuitable for very deep wells, as the mechanical force required to lift fluid from greater depths becomes too high for the system.
Not Ideal for High Gas-to-Oil Ratios: If the well produces significant gas, it can hinder the effectiveness of a beam pump.
Space Requirements: The large surface equipment of a beam pump requires considerable space, which may not be feasible in specific locations,
Cycle Interference: If the pump operates at very low flow rates, the mechanical cycles can become inefficient.
Mechanical Wear: Over time, the sucker rods and other mechanical components can experience wear and tear.
Electric Submersible Pump (ESP)
This is one of the most widely used artificial lift systems in the oil and gas industry, particularly for high-production wells that require lifting oil and gas from significant depths. The ESP consists of a motor and a multistage pump located downhole.
An ESP system works by utilizing a submersible electric motor connected to a series of multistage centrifugal pumps. These pumps are installed in the wellbore and submerged in the produced fluid.
ESPs are typically used in wells that meet certain criteria:
Deep wells: ESPs can be used in wells with greater depths (ranging from 1,500 to 10,000 feet or more).
High-production rate wells: ESPs are ideal for wells that require high flow rates (hundreds or even thousands of barrels per day).
High fluid volumes: They are particularly useful when lifting large fluid volumes, such as oil with lower viscosity or water-producing wells.
Pros of Electric Submersible Pumps
High Production Rates: They are designed to lift large volumes of fluid, making them ideal for wells with high production capacity. ESPs can maintain consistent performance and provide steady production.
Compact Design: They require minimal surface space, making them suitable for use in locations with space constraints. The system is particularly beneficial for offshore platforms and other areas with limited surface space.
Cons of Electric Submersible Pumps
Sensitivity to Gas and Solids: Gas production can reduce the pump's efficiency, as gas bubbles may interfere with the pump's ability to lift liquid. ESPs are not ideal for wells with high solids levels, as they can wear down the pump’s components.
Energy Requirements: They require significant electrical power to operate, particularly when lifting from deep wells, resulting in high operating costs.
Gas Lift
Gas lift is an artificial lift system that uses injected gas to reduce the density of the produced fluids (oil, gas, and water), thereby assisting in lifting them to the surface.
Overview of Gas Lift Systems and Injection Mechanisms
The basic principle of gas lift is straightforward: gas is injected into the well at specific points in the production tubing, reducing the hydrostatic pressure of the fluids and allowing them to flow to the surface more easily.
This works by lowering the density of the fluid column, effectively "lightening" the fluids, which aids in overcoming the natural pressure at the surface and allows for more efficient production.Gas lift systems are particularly well-suited for wells with a high gas-to-oil ratio (GOR), as they rely on gas injection to lift the fluids to the surface.
Advantages of Gas Lift Systems
Flexibility: They are highly flexible and can be adapted to different conditions. For example, the amount of gas injected into the well can be controlled, allowing for adjustments based on production rates, reservoir pressure, and fluid characteristics.
Ability to Handle Deviated and Horizontal Wells: This is a great choice for wells in challenging wellbore geometries, such as those in offshore fields or deep reservoirs with non-vertical drilling trajectories.
Progressive Cavity Pump (PCP)
The Progressive Cavity Pump (PCP) is a positive displacement pump widely used in the oil and gas industry to lift and transport fluids, especially in challenging well conditions. It is particularly effective in applications where high-viscosity fluids, such as heavy oil or fluids containing solids, are being produced. The PCP operates based on a unique mechanism that provides steady, continuous flow, even in demanding environments.
The Progressive Cavity Pump consists of two main components:
Rotor: The rotor is a helical screw-like component that rotates within the stator. It is usually made of high-strength, corrosion-resistant materials to withstand harsh operating conditions.
Stator: The stator is a stationary, rubber-lined component with a helical cavity that matches the shape of the rotor. The stator’s inner surface is designed to create tight contact with the rotor, ensuring that the fluids are moved in a consistent, progressive motion through the pump. As the rotor turns inside the stator, fluid is trapped between the two components and transported upward in a continuous flow.
This design allows for positive displacement, meaning that the pump moves a fixed amount of fluid per revolution of the rotor, providing a steady and consistent flow. This mechanism makes PCPs particularly suited for handling fluids with a high viscosity, such as heavy oils, and those containing solids or gas.
Applications:
Heavy Oil Production: PCPs are often used in fields where heavy crude oil with high viscosity is produced. Since PCPs can handle these thick fluids more efficiently than other lift systems, they help ensure continuous production in heavy oil reservoirs.
Well Conditions with High Solids Content: PCPs are well-suited for wells that produce fluids with high amounts of sand or solids, as their unique mechanism can handle these abrasive particles without significant damage. This makes them ideal for wells where other lift systems might experience blockages or wear and tear.
Low-Pressure Wells: PCPs are often used in low-pressure wells or fields where conventional artificial lift systems (such as beam pumps or ESP systems) may not be effective due to insufficient reservoir pressure. The PCP can provide a reliable and efficient method for lifting oil from these reservoirs.
Gas-Lift Assisted Wells: In some cases, PCPs are used in combination with gas lift systems to improve fluid handling and reduce the overall energy consumption of the lifting process.
Produced Water Handling: In wells with a high water cut (produced water alongside oil), PCPs can be used to lift both the oil and water together, providing a cost-effective solution for handling mixed fluids.
Strengths of Progressive Cavity Pumps
Handling Heavy Oil: The positive displacement mechanism allows the pump to maintain a consistent flow of thick liquids, making it ideal for heavy oil fields.
Handling Solids and Abrasive Fluids: They are well-suited for handling fluids with solids without clogging or causing significant damage to the pump.
Weakness of Progressive Cavity Pumps
Limited to Lower Flow Rates: They are generally suited for lower flow rates compared to other artificial lift systems. They are typically not capable of handling the high flow rates required for large, high-production wells.
Hydraulic Pumping Systems
Hydraulic pumping systems use pressure from a fluid, typically a high-pressure liquid, to drive a pump mechanism that moves production fluids to the surface.
Hydraulic pumping systems primarily come in two forms:
Jet pump: A jet pump is a type of hydraulic pump that utilizes a high-velocity jet of fluid to create a suction effect that lifts production fluids to the surface.
Piston pump: It is a type of positive displacement pump that uses a piston mechanism to lift fluid from the well. The system operates by using the reciprocating motion of a piston inside a cylinder to displace the production fluid and move it upward.
Jet pumps
They are commonly used in deep wells, where the pressure and depth make other lift systems less effective.
They are beneficial in wells with significant gas content, as they can handle gas and liquid mixture efficiently.
Piston pumps
They are well-suited for wells with thick or viscous fluids like heavy oil.
They are effective in high-pressure wells, as they can create high suction to lift fluids in deep reservoirs
Considerations for Maintenance and Cost
Jet Pumps: Jet pumps have fewer moving parts, making them simpler to maintain. However, the nozzles and diffusers may become worn over time. So, regular monitoring and replacement of these components are required.
Jet pumps have a lower initial cost compared to piston pumps, which involve more intricate mechanical parts and installation requirements.Piston Pumps: Piston pumps involve more moving parts. The reciprocating action can lead to mechanical fatigue. Seals and valves also require frequent inspection and replacement.
While jet pumps are simple, they tend to have higher operating costs due to the need for a high-pressure fluid supply.
Plunger Lift
Plunger lift is an intermittent artificial lift system that uses a plunger to lift fluids from the wellbore.
How Plunger Lift Works in Intermittent Production
The system involves a plunger, which is a solid, cylindrical device that moves up and down the wellbore.
The plunger lift system works intermittently, meaning the well is not continuously producing fluids. The plunger is released periodically to perform a lifting action, creating batches of fluid production, which is typical in wells with intermittent or low-pressure production.
Ideal Conditions for Plunger Lift Usage
Here are some ideal conditions for plunger lift usage:
Wells with High Gas-to-Liquid Ratios: They are best suited for wells where gas is the primary driver of fluid movement.
Wells with Intermittent or Low-Pressure Production: They are particularly effective for wells that produce at low flow rates or where production does not occur continuously.
Wells with High Water Cut: In wells with a high water cut, the plunger lift can assist in lifting both water and oil.
Cost-Effectiveness and Efficiency
Marginal and Mature Wells: They are a great choice where wells often experience lower pressures and have intermittent production.
Low-Volume, Low-Pressure Wells: They can improve production rates without the need for a larger-scale, more expensive artificial lift system.
Offshore and Remote Wells: They are highly advantageous as they don’t require external power, reducing both installation costs and operating expenses.
#Comparing Artificial Lift Systems
When selecting an artificial lift system, operators must assess various factors to ensure that the chosen system meets the well's specific needs.
Performance Matrix:
Cost Analysis: Initial investment vs. long-term operational costs.
Flexibility: Adapting to changing production rates and reservoir conditions.
#Common Challenges and How to Overcome Them
Artificial lift systems are essential for maintaining production rates, but they come with specific challenges that operators must address.
Identifying Mismatches Between the Lift System and Well Conditions
Challenge:
Selecting the wrong artificial lift system can lead to inefficiency, higher operational costs, and reduced production. Mismatches may arise when there are discrepancies between the system’s capabilities and factors.
Solutions:
Detailed Well Analysis: Conduct a thorough well assessment and reservoir analysis to understand key characteristics. This will ensure the lift system chosen aligns with the well's conditions.
Consultation with Experts: Work with engineering teams or artificial lift specialists to ensure the selected system will optimize performance based on reservoir dynamics.Managing Maintenance and Downtime Issues
Challenge:
Maintenance is a significant concern as wear and tear, mechanical failure, and the harsh conditions of the well can result in unplanned downtime. This can lead to lost production, high repair costs, and extended interruptions in operation.
Solutions:
Predictive Maintenance: Use real-time monitoring and data analytics to predict failures before they occur. This helps identify when parts need to be replaced or adjusted.
Regular Inspections and Service: Create a preventive maintenance schedule for the lift system, including regular inspections, lubrications, and replacement of worn parts.
Adapting to Evolving Field Dynamics (e.g., Water Cut Increases)
Challenge:
As production continues over time, the field dynamics change. For instance, the water cut may increase, the reservoir pressure may decrease, or there may be higher gas-to-oil ratios.
Solutions:
Flexible Lift System Design: Choose a lift system that is scalable and adaptable to handle changes in fluid composition.
Adaptive Controls: Implement adaptive control systems that can adjust pump operation based on real-time data from the well.
#Real-World Examples and Case Studies
Let's explore some successful implementations and lessons learned from poorly matched systems, to provide a more practical understanding of how different artificial lift systems are applied in real-world scenarios.
Successful Implementation of Gas Lift in a North Sea Oil Field
Scenario:
In a North Sea oil field, the operator faced fluctuating well production rates and a changing gas-to-oil ratio as the reservoir matured.
Solution:
A gas lift system was chosen because it was adaptable to fluctuating production rates and increased gas content in the reservoir. The gas lift system used produced gas from the field to maintain sufficient lifting power, and the injection rates were adjusted in real-time to suit changes in well conditions.
Flexibility is key in mature fields, mainly when dealing with declining pressures or changing fluid compositions.
In this case, the importance of real-time monitoring and adaptive systems was highlighted, as they allowed for efficient gas management and reduced production losses.
Beam Pump in a Texas Oil Field
Scenario:
In a Texas oil field, an operator decided to use a beam pump for a deep well with moderate fluid production. Over time, the operator noticed that production rates began to fluctuate, and the well produced a mix of oil, water, and gas.
Solution:
The operator switched to a gas lift system, which was better suited to manage the well's intermittent production and varying gas content. The gas lift system provided the flexibility needed to maintain production, even with fluctuating fluid types.
Conclusion:
Mismatching systems to well dynamics (e.g., gas presence) can lead to increased costs and decreased efficiency.
Gas lift is often the better choice when dealing with wells that experience intermittent production or fluctuating gas content.The Role of Technology in Artificial Lift
As the oil and gas industry evolves, technological advancements are increasingly important in improving the efficiency, reliability, and performance of artificial lift systems.
Below are the key areas where technology is driving progress in artificial lift systems.
Innovations in Automation and Remote Monitoring
Automation and remote monitoring technologies are transforming the way artificial lift systems are managed. These technologies enable operators to monitor well performance in real-time, identify issues early, and take proactive actions, often without the need for on-site intervention.
Predictive Maintenance and AI-Driven Decision-Making
Predictive maintenance uses advanced analytics, machine learning, and artificial intelligence (AI) to forecast potential failures and schedule maintenance before they occur. By analyzing data collected from artificial lift systems, predictive maintenance helps operators improve system uptime and reduce costly unplanned repairs.
Advanced Materials Improving Durability and Performance
The development of advanced materials is enhancing the durability and performance of artificial lift systems. These materials are designed to withstand extreme pressures, temperatures, and abrasive environments, which are common in oil and gas wells.
#Environmental and Sustainability Considerations
As the oil and gas industry moves toward more energy-efficient and environmentally friendly practices, artificial lift systems are evolving to reduce their carbon footprint and improve resource management.
How Artificial Lift Systems Contribute to Energy Efficiency
The energy efficiency of these systems is a critical factor in minimizing their operational impact and ensuring long-term sustainability.
The key factors in energy efficiency are:
Optimized power usage
Reduced energy consumption in well operations
Integration with renewable energy sources
Use of smart technologies
Strategies to Minimise Environmental Impact During Operations
Minimizing the environmental impact of artificial lift systems involves strategies that focus on reducing emissions, minimizing resource consumption, and mitigating the risk of spills or contamination.
The key strategies include:
Zero-Flaring Technologies
Energy Recovery and Reuse
Minimising Water Use
Reducing Noise and Vibration
The Role of Lift Systems in Enabling Enhanced Oil Recovery (EOR) Techniques:
Artificial lift systems also play a significant role in Enhanced Oil Recovery (EOR) techniques, which are employed to increase the recovery factor of oil reservoirs.
The key EOR techniques include:
Gas Injection
Water Flooding
Chemical Flooding
Thermal EOR
Operators who embrace these innovative technologies and sustainable practices will be better equipped to meet future energy demands while minimising their operations' environmental impact.
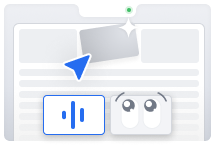